-
Currency:Localize your Content
You can set your preferred currency for this account.
Choose a Currency
Currency- CHOOSE YOUR CURRENCY
Update Currency
Changing Currency will cause your current cart to be deleted. Click OK to proceed.
To Keep your current cart, click CLOSE and then save your cart before changing currency.
-
Select Account
Switching accounts will update the product catalog available to you. When switching accounts, your current cart will not move to the new account you select. Your current cart will be available if you log back into this account again.
Account# Account Name City Zip/Post Code CANCELPROCEEDMy Account -
-
Products
- View All Control & Supervisory Systems
- Control & Supervisory Systems Parts & Accessories
- Distributed Control Systems (DCS)
- Safety Systems
- SCADA
- Quality Control Systems (QCS)
- Modular Controllers
- Human Machine Interfaces (HMI)
- Remote Terminal Units (RTU)
- Drives
- Modular Systems Remote IO
- Discrete Automation Solutions
- View All Field Instruments
- Pressure Transmitters
- Temperature Transmitters
- Multivariable Transmitters
- Wireless Transmitters
- Level Transmitters
- Flow Meters
- Honeywell Versatilis™ IOT Sensor Solutions
- RMA Remote Meter Assemblies
- Field Instruments Configuration Tools and Software
- Discontinued: Field Instruments
- View All Discontinued: Field Instruments
- SmartLine RM Series - Guided Level Meters
- SmartLine RM Series - Non-Contact Radar Level Meter
- XYR 6000 Absolute Pressure
- XYR 6000 Differential Pressure
- XYR 6000 Discrete I/O
- XYR 6000 Gauge Pressure
- XYR 6000 High Level Analog Input Transmitter
- XYR 6000 Temperature Transmitters
- XYR 6000 Universal I/O
- View All Regulators & Safety Accessories
- High Pressure Regulators up to ANSI 600
- High Pressure Regulators up to PN40 (ANSI 300)
- Medium Pressure Regulators up to PN16 (ANSI 150)
- Pilot Heater
- Safety Relief Valves
- Safety Shut-Off Valves
- Series 200 Small Pressure Regulators (Pressure Reducer)
- Series 600 Control Equipment for Safety Shut-Off Valves
- Series 600 Pilot Regulators for Pilot operated Gas Pressure Regulators
- Series 900 - Gas filters/Valves and other Components
- Regulators & Safety Accessories Spare Parts
- View All Fixed Gauging
- PL3700X Pressure and Level Transmitters
- EM540 & EM940 Radar Level Gauge
- T901 Temperature and Pressure Transmitters
- Lidec Liquid Level Switch
- CT801 Electropneumatic Level Transmitters
- Communication Interface Unit
- CargoBoss Tank Gauging Software
- Q96 Analog Indicator
- Spare Parts & Accessories - Marine Fixed Gauging
- View All Portable Sampling
- HERMetic Sampler GT & Sampler GT Chem for Marine Applications
- HERMetic Sampler GT1 for Marine Applications
- HERMetic Sampler GTX for Marine Applications
- HERMetic Sampler GTN for Marine Applications
- HERMetic Sampler GT4 for Marine Applications
- Gauging and Sampling for high-pressure Tankers
- HERMetic Samplers for Restricted Operations
- Spare Parts - Marine Portable Gauging & Sampling
- Ballast Water Sampler
- View All Marine Pressure Transmitters
- SmartLine STF800 - Flange Mount
- SmartLine STA800 - Absolute Pressure
- Absolute Pressure Transmitter - SmartLine STA700
- Remote Diaphragm Transmitters - SmartLine STR700
- SmartLine STR800 - Remote Diaphragm
- SmartLine STD800 - Differential Pressure
- Differential Pressure Transmitter - SmartLine STD700
- Gauge Pressure Transmitters - SmartLine STG700
- SmartLine STG800 - Gauge Pressure
- Flange Mount Transmitters - SmartLine STF700
- View All Discontinued: Process Instruments
- DCP50 DIN Programmer
- DL4000 Conductivity Cells
- DL5000 Equilibrium Probe
- 7774/7774D Insertion/Removal Ball Valve Mounting
- 7777/7777D Immersion/In-Line Glass Mounting
- 7777DVP Immersion/In-Line Mounting
- DL1000 Durafet Mountings
- DL2000 Meredian Glass Mountings
- DL3000 ORP Mountings
- HB and HBD Series Ruggedized Electrodes
- DR4300 Circular Chart Recorder
- UDC700 DIN Controller
- Process Instrument Explorer (PIE) Software
- Honeywell’s Chamber IQ
- 4905 Immersion or Flow Thru Mounting
- 4909 Ball Valve or Insertion Mounting
- 4973 Flow Thru Mounting
- View All Portable Gauging & Sampling for Land Applications
- HERMetic UTImeter Gtex 2000 - Closed Type - Land Applications
- HERMetic UTImeter Otex - Restricted Type - Land Applications
- HERMetic Sampler GT & Sampler GT Chem - Land Applications
- HERMetic Sampler GTX Chem - Land Applications
- HERMetic Sampler GTN Chem - Land Applications
- HERMetic Sampler GT4 - Land Applications
- HERMetic Sampler A-2 and A-4 - Land Applications
- View All Burners & Heat Exchangers
- Direct Fired Furnace Burners
- Self-Recuperative and Radiant Tube Burners
- Single Burners
- Line & Duct Burners
- Glass & Oxygen Burners
- Immersion Tube Burners
- Hauck Asphalt Burners
- Exothermics Heat Exchangers & Indirect Air Heaters
- Pre-Mix Equipment
- Pilot Burners
- Burner Accessories
- Discontinued: Burners & Heat Exchangers
- View All SmartLine ST700 Pressure Transmitters
- Flange Mount Transmitters - SmartLine STF700
- Gauge Pressure Transmitters - SmartLine STG700
- Absolute Pressure Transmitter - SmartLine STA700
- Flush Mount Pressure Transmitters - SmartLine ST700
- Remote Diaphragm Transmitters - SmartLine STR700
- Differential Pressure Transmitter - SmartLine STD700
- View All Meter Hardware & Accessories
- Hand Tools and Toolkits
- Needle Valves
- Swivel Washers
- Pete's Plugs
- Differential Pressure Testers
- Gas Leak Detectors
- Shut-Off Seals
- Batteries
- Meter Nuts
- Manometers
- M201E DP Tester
- Paint Covers
- Pressure Gauges
- Lubrication & Oil
- Meter Swivels
- Dust Caps
- Straightening Vanes
- Meter Connections
- Critical Flow Provers
- Meter Adapters
- Pulsers & Displays
- Flange Covers
- Splashguards
- View All Discontinued: Burners & Heat Exchangers
- EcoStar IIB
- ImmersoPak
- Blast Tips
- Eclipse Pilots
- ThermJet Self-Recuperative Burner
- WIDE-RANGE®
- CCTV
- ValuPak
- GTCPA
- OvenPak II
- Delta-TE
- GT-NG
- 780P
- Kinedizer
- ExtensoJet
- MultiFire
- Forehearth Burners
- Sealed Nozzle
- SVG
- Oxy-Therm® FH
- LP, Tee, Vari-Set Mixers
- WRASP
- INCINO-PAK®
- CYCLOMAX®
- 03FA
- AirJector
- Brightfire (Original)
- View All Burner Control Units
- Honeywell 7800 SERIES burner control unit
- Honeywell SLATE combustion management system
- Burner control unit BCU 570
- Burner control units BCU 560, BCU 565, BCU 580
- Automatic burner control units PFU
- Protective system control FCU
- Kromschroeder IFD 258 burner control unit
- Kromschroeder IFD 244 burner control unit
- SOLA
- Legacy Burner Management Systems
- BCU 4 (Next Generation)
- Burner control unit BCU 370
- View All Industrial Flame Monitoring (IFM)
- Flare Stack Monitoring System Watchdog III
- Industrial Flame Monitoring Accessories
- Gas Igniters GHE
- Viewing Heads S70X/S80X
- FASA Glass and Quartz Fiber Optics
- Signal Processors Model P522
- Signal Processors Model 600U
- Viewing Heads S55XBE
- Viewing Heads U2
- Signal Processors Model 700SP
- FlameTools or Thermalsoft Configuration Tools
- Advanced Viewing Heads S650
- Advanced Signal Processors P650
- Signal Processors Model P531 or P532
- View All Discontinued: Burner Management Systems
- Kromschroeder BCU 400 burner control unit
- Automatic burner control units IFS 132B, 135B, 137B
- R4343 Flame Switch
- Ignition Transformers Q652
- Impulse system MPT 700
- Flame detector IFW 15
- Flame detector for continuous operation IFW 50
- Automatic burner control units PFS 778, 748
- Flame detectors PFF
- Ultraviolet Flame Detector C7927
- Ultraviolet Flame Detector C7961E,F
- Automatic burner control units for continuous operation PFD 778
- Automatic burner control units IFS 110IM, 111IM
- IFD 450, 454
- View All Manual Valves & Filters
- Manual valves AKT
- Manual valves with thermal equipment trip AKT..TAS
- Thermal equipment trips TAS
- Gas-filters GFK
- A Style Synchro Valves
- Disc Type Check Valves
- Flow adjusting cocks GEHV, GEH, LEH
- Manual Shutoff Valves
- Shut off valves ZIVA
- Adjustable Orifice Valves (ALO/ALO-R)
- View All Pressure Regulators
- Pressure regulators for gas J78R, 60DJ
- Pressure regulators for gas GDJ
- Pressure regulators for gas VGBF
- Safety shut-off valves JSAV
- Relief valve VSBV
- Variable air/gas ratio controls GIKH
- Circulation pressure control and relief regulators VAR
- Gas Pressure Regulators Maxon
- Air/gas ratio controls GIK
- View All Shutoff Valves
- Series 8000 Air Actuated Safety Shut-off Valves for Fuel Gas Service
- Series 8000 Air Actuated Safety Shutoff Valves for Liquid Service
- High Pressure Electro-Mechanical Gas Safety Shut-off Valves
- High Pressure Electro-Mechanical Oil Safety Shut-off Valves
- NI Series Hazardous Location Safety Shut-off Valves
- V5097 Integrated gas valve train
- V48/V88 Diaphragm gas valves
- V4943/V8943 Single-stage pressure regulating valves
- V4944B, L, N/8944B, C, L, N Two-stage pressure regulating gas valves
- V5055 Industrial gas valves, V4055 Fluid power actuators
- V4062 Fluid power actuators
- Solenoid valves for gas VGP
- Solenoid valves for gas VG
- Motorized valves for gas VK
- Solenoid valves for gas VE, V4295
- VQ400/800 Series
- V4046/V8046 Pilot gas valves
- View All Butterfly Valves & Actuators
- BV-Pak
- Butterfly valves BVG, BVA, BVH
- Linear flow controls IFC, VFC
- Butterfly valves DKR
- Butterfly Valves
- Solenoid-operated butterfly valves for air MB 7/BVHM
- Wafer Butterfly Valves for Hot Air WBV-H
- Honeywell Slate low torque actuator
- Modutrol Motors
- Kromschröder IC + Valve Assemblies
- Actuators IC
- View All Pressure Switches & Gauges
- Honeywell C6097 pressure switches for gas
- Kromschroeder DL..A pressure switches for air
- Kromschroeder DG pressure switches for gas
- Kromschroeder DL..K pressure switches for air
- Kromschroeder DG..C pressure switches for gas
- Kromschroeder DL..E pressure switches for air
- Elektronic pressure gauge DMG
- Pressuretrol® Limit controllers L4079A, B, W, L604N
- Pressure gauges KFM, RFM
- Pressure Indicators PI
- PressureTrol® Pressure monitoring on/off controllers L404F, T, V
- PressureTrol® Pressure monitoring modulating controllers L91A, B
- CPS
- Pressure switches for gas DGM, DWR
- Vaporstat ® Controllers L408J
-
Services
Services
-
Cybersecurity Services
Highly skilled OT cybersecurity consultants can provide services to support your cybersecurity needs.
-
Fire & Gas Services
Process fire and gas systems play a key role in protecting valuable production assets.
-
Control System Services
Modernize systems, optimize performance, and help mitigate cybersecurity risks.
-
Combustion Services
Technical services and engineered solutions for fuel-fired equipment across all major industries.
-
Training
Honeywell Academy offers a variety of courses to keep your workers updated on the latest technology.
-
Utility Services
Industry services, including: AMI upgrades, gas line locating, and water leak detection.
-
Smart Grid Solutions & Services (SGS)
Comprehensive energy efficiency solutions for the Utility Industry
-
Maintenance Assist
Maintenance Assist is Honeywell’s advanced Generative AI digital assistant designed to streamline maintenance tasks and enhance efficiency.
-
Cybersecurity Services
-
Solutions
Solutions
-
Support
Support
You are browsing the product catalog for
You are viewing the overview and resources for
Get Super Powered with SmartLine
Fast Track Automation in Pharmaceutical Manufacturing
By Steve Zarichniak, Technical Solutions Consultant, Honeywell Process Solutions
There’s no doubt that pharmaceutical companies are under pressure to produce a wider range of products, and deliver higher quality, with fewer resources. Production sites must be more agile, with the capability to react to changing demands quickly.
Increasingly, drug manufacturers are turning to advanced automation technologies and project execution methodologies to compress engineering time, reduce inefficiencies and enable Parallel Planning.
Throughout the global pharmaceutical industry, there is a need to accelerate the delivery of medical solutions to patients by helping ensure more efficient production and testing capabilities along with facilitating a strengthened supply chain.
Leading manufacturers have made it a strategic initiative to go from development to production faster, with reduced cost and effort. Their specific objectives include:
· Expediting new drugs and therapies to commercial production; and
· Implementing scalable solutions for flexible manufacturing.
Today, pharmaceutical companies are intentionally manufacturing new drugs “at-risk,” meaning the product is produced at commercial scale before final regulatory approval. Shipment of the product can then occur immediately upon approval. Fast track implementations provide a stable, compliant, and exceptionally expedient methodology to achieve this end.
Innovative Approach to Deploying Automation
Experience has shown the most effective way to expedite production of new pharmaceutical products is to facilitate the design of full commercial-scale manufacturing earlier, while therapies are still in clinical trials.
Leading technology providers have developed “fast track” automation solutions that can be configured in a virtual environment and then implemented once a drug is approved and ready to be produced for patients. With this approach, plants can rapidly deploy out-of-the-box GxP-compliant automation solutions supporting 21CFR Part 11 across their production lines while reducing associated risk.
Pharmaceutical producers can now utilize flexible automation system builds with pre-structured engineering design scenarios based on whether legacy equipment will be repurposed, or new equipment installed. The typical automation scenarios, based on standardized GAMP5 Model definitions, include:
· SCADA with manual data entry and manually driven control;
· SCADA over process skids that require manual and/or automated controls;
· DCS with new process skids; and
· DCS with a mix of new and repurposed units.
Combinations of the pre-structured systems can be used to address the control requirements of individual units and skids, or even the entire process train. To further support the pre-structured designs, some automation suppliers offer solutions enabling an existing SCADA system to seamlessly evolve into a full-fledged DCS.
Fast track automation allows users to start critical production system development activities earlier and perform them in parallel in the cloud, and using virtual engineering, physically bind them at the manufacturing facility. This process, plus flexible I/O, allows late-stage configuration as the final step. The result is significantly reduced engineering time and effort, as well as faster ramp-up to full production.
Results from successful industry projects indicate that lean execution methodologies inherent in fast-track automation can speed up implementation and help to simplify final configuration. They enable at-risk manufacturing planning to begin during final Phase 3 clinical trials, using a single interface providing visibility across start-up and ongoing operations.
Technologies for Expediting Production Flexibility
Throughout the pharmaceutical field, new technology advancements are driving an improved end-to-end manufacturing process. The tools and solutions serving as fast-track enablers for flexible production include:
· Digital Twins (Virtual Engineering)
· Batch in the Controller
· Control from the Data Center
· Flexible Input/Output (I/O)
· Orchestration Layer Connectivity
· MES Seamless Interactions
· Advanced Analytics
For example, digital twin technology supports parallel process automation development paths, making it possible to create a software-driven, cloud-based digital representation of production processes and assets using process simulation and validate the design in the cloud. Production systems can be configured in the cloud so that when expanded or modified operations are required, users simply access the database, without having to revalidate, and deploy the replicated system within a new production line.
The unique ability to execute a full S88 batch model in the process controller reduces the engineering effort required to design, modify, and configure a batch system. With batch running in a cloud-based controller and not in the server, an orchestration layer can be employed for direct batch automation with multiple production skids. This layer simplifies integration with legacy sub-systems and can support enhanced GxP compliance.
Impact on Pharmaceutical Manufacturers
Using the power of the cloud, virtualization, pre-designed automation solutions, adaptable I/O, remote asset management from a data center and efficient project implementation, pharmaceutical companies can prepare automation designs in parallel with clinical trials so production can be quickly mobilized once a therapy is ready for commercial scale-up.
The impact of fast-track automation on drug manufacturers includes:
· Greater confidence when undertaking at-risk manufacturing;
· Enhanced virtual simulation reducing validation effort;
· Shorter time to complete design and engineering; and
· Quick response to product demand fluctuation.
By employing the latest generation of automation tools and solutions, coupled with modular facility construction, pharmaceutical companies can go from trial and approval to production in significantly less time.
Copyright © 2025 Honeywell International Inc.
Maximum File Size
Maximum Files Exceeded
Due to inactivity you will be logged out in 000 seconds.
Maximum File Size
Maximum Files Exceeded
Honeywell International Inc. is committed to ensuring compliance with global laws that regulate its export and import activities. In following company procedures, it has been determined that is identified on a denied/restricted parties list that is applicable to this transaction.
As a result, Honeywell is unable to continue with this request.
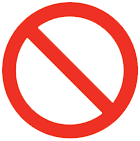