-
Currency:Localize your Content
You can set your preferred currency for this account.
Choose a Currency
Currency- CHOOSE YOUR CURRENCY
Update Currency
Changing Currency will cause your current cart to be deleted. Click OK to proceed.
To Keep your current cart, click CLOSE and then save your cart before changing currency.
-
Select Account
Switching accounts will update the product catalog available to you. When switching accounts, your current cart will not move to the new account you select. Your current cart will be available if you log back into this account again.
Account# Account Name City Zip/Post Code CANCELPROCEEDMy Account -
-
Products
- View All Control & Supervisory Systems
- Control & Supervisory Systems Parts & Accessories
- Distributed Control Systems (DCS)
- Safety Systems
- SCADA
- Quality Control Systems (QCS)
- Modular Controllers
- Human Machine Interfaces (HMI)
- Remote Terminal Units (RTU)
- Drives
- Modular Systems Remote IO
- Discrete Automation Solutions
- View All Field Instruments
- Pressure Transmitters
- Temperature Transmitters
- Multivariable Transmitters
- Wireless Transmitters
- Level Transmitters
- Flow Meters
- Honeywell Versatilis™ IOT Sensor Solutions
- RMA Remote Meter Assemblies
- Field Instruments Configuration Tools and Software
- Discontinued: Field Instruments
- View All Discontinued: Field Instruments
- SmartLine RM Series - Guided Level Meters
- SmartLine RM Series - Non-Contact Radar Level Meter
- XYR 6000 Absolute Pressure
- XYR 6000 Differential Pressure
- XYR 6000 Discrete I/O
- XYR 6000 Gauge Pressure
- XYR 6000 High Level Analog Input Transmitter
- XYR 6000 Temperature Transmitters
- XYR 6000 Universal I/O
- View All Regulators & Safety Accessories
- High Pressure Regulators up to ANSI 600
- High Pressure Regulators up to PN40 (ANSI 300)
- Medium Pressure Regulators up to PN16 (ANSI 150)
- Pilot Heater
- Safety Relief Valves
- Safety Shut-Off Valves
- Series 200 Small Pressure Regulators (Pressure Reducer)
- Series 600 Control Equipment for Safety Shut-Off Valves
- Series 600 Pilot Regulators for Pilot operated Gas Pressure Regulators
- Series 900 - Gas filters/Valves and other Components
- Regulators & Safety Accessories Spare Parts
- View All Fixed Gauging
- PL3700X Pressure and Level Transmitters
- EM540 & EM940 Radar Level Gauge
- T901 Temperature and Pressure Transmitters
- Lidec Liquid Level Switch
- CT801 Electropneumatic Level Transmitters
- Communication Interface Unit
- CargoBoss Tank Gauging Software
- Q96 Analog Indicator
- Spare Parts & Accessories - Marine Fixed Gauging
- View All Portable Sampling
- HERMetic Sampler GT & Sampler GT Chem for Marine Applications
- HERMetic Sampler GT1 for Marine Applications
- HERMetic Sampler GTX for Marine Applications
- HERMetic Sampler GTN for Marine Applications
- HERMetic Sampler GT4 for Marine Applications
- Gauging and Sampling for high-pressure Tankers
- HERMetic Samplers for Restricted Operations
- Spare Parts - Marine Portable Gauging & Sampling
- Ballast Water Sampler
- View All Marine Pressure Transmitters
- SmartLine STF800 - Flange Mount
- SmartLine STA800 - Absolute Pressure
- Absolute Pressure Transmitter - SmartLine STA700
- Remote Diaphragm Transmitters - SmartLine STR700
- SmartLine STR800 - Remote Diaphragm
- SmartLine STD800 - Differential Pressure
- Differential Pressure Transmitter - SmartLine STD700
- Gauge Pressure Transmitters - SmartLine STG700
- SmartLine STG800 - Gauge Pressure
- Flange Mount Transmitters - SmartLine STF700
- View All Discontinued: Process Instruments
- DCP50 DIN Programmer
- DL4000 Conductivity Cells
- DL5000 Equilibrium Probe
- 7774/7774D Insertion/Removal Ball Valve Mounting
- 7777/7777D Immersion/In-Line Glass Mounting
- 7777DVP Immersion/In-Line Mounting
- DL1000 Durafet Mountings
- DL2000 Meredian Glass Mountings
- DL3000 ORP Mountings
- HB and HBD Series Ruggedized Electrodes
- DR4300 Circular Chart Recorder
- UDC700 DIN Controller
- Process Instrument Explorer (PIE) Software
- Honeywell’s Chamber IQ
- 4905 Immersion or Flow Thru Mounting
- 4909 Ball Valve or Insertion Mounting
- 4973 Flow Thru Mounting
- View All Portable Gauging & Sampling for Land Applications
- HERMetic UTImeter Gtex 2000 - Closed Type - Land Applications
- HERMetic UTImeter Otex - Restricted Type - Land Applications
- HERMetic Sampler GT & Sampler GT Chem - Land Applications
- HERMetic Sampler GTX Chem - Land Applications
- HERMetic Sampler GTN Chem - Land Applications
- HERMetic Sampler GT4 - Land Applications
- HERMetic Sampler A-2 and A-4 - Land Applications
- View All Burners & Heat Exchangers
- Direct Fired Furnace Burners
- Self-Recuperative and Radiant Tube Burners
- Single Burners
- Line & Duct Burners
- Glass & Oxygen Burners
- Immersion Tube Burners
- Hauck Asphalt Burners
- Exothermics Heat Exchangers & Indirect Air Heaters
- Pre-Mix Equipment
- Pilot Burners
- Burner Accessories
- Discontinued: Burners & Heat Exchangers
- View All SmartLine ST700 Pressure Transmitters
- Flange Mount Transmitters - SmartLine STF700
- Gauge Pressure Transmitters - SmartLine STG700
- Absolute Pressure Transmitter - SmartLine STA700
- Flush Mount Pressure Transmitters - SmartLine ST700
- Remote Diaphragm Transmitters - SmartLine STR700
- Differential Pressure Transmitter - SmartLine STD700
- View All Meter Hardware & Accessories
- Hand Tools and Toolkits
- Needle Valves
- Swivel Washers
- Pete's Plugs
- Differential Pressure Testers
- Gas Leak Detectors
- Shut-Off Seals
- Batteries
- Meter Nuts
- Manometers
- M201E DP Tester
- Paint Covers
- Pressure Gauges
- Lubrication & Oil
- Meter Swivels
- Dust Caps
- Straightening Vanes
- Meter Connections
- Critical Flow Provers
- Meter Adapters
- Pulsers & Displays
- Flange Covers
- Splashguards
- View All Discontinued: Burners & Heat Exchangers
- EcoStar IIB
- ImmersoPak
- Blast Tips
- Eclipse Pilots
- ThermJet Self-Recuperative Burner
- WIDE-RANGE®
- CCTV
- ValuPak
- GTCPA
- OvenPak II
- Delta-TE
- GT-NG
- 780P
- Kinedizer
- ExtensoJet
- MultiFire
- Forehearth Burners
- Sealed Nozzle
- SVG
- Oxy-Therm® FH
- LP, Tee, Vari-Set Mixers
- WRASP
- INCINO-PAK®
- CYCLOMAX®
- 03FA
- AirJector
- Brightfire (Original)
- View All Burner Control Units
- Honeywell 7800 SERIES burner control unit
- Honeywell SLATE combustion management system
- Burner control unit BCU 570
- Burner control units BCU 560, BCU 565, BCU 580
- Automatic burner control units PFU
- Protective system control FCU
- Kromschroeder IFD 258 burner control unit
- Kromschroeder IFD 244 burner control unit
- SOLA
- Legacy Burner Management Systems
- BCU 4 (Next Generation)
- Burner control unit BCU 370
- View All Industrial Flame Monitoring (IFM)
- Flare Stack Monitoring System Watchdog III
- Industrial Flame Monitoring Accessories
- Gas Igniters GHE
- Viewing Heads S70X/S80X
- FASA Glass and Quartz Fiber Optics
- Signal Processors Model P522
- Signal Processors Model 600U
- Viewing Heads S55XBE
- Viewing Heads U2
- Signal Processors Model 700SP
- FlameTools or Thermalsoft Configuration Tools
- Advanced Viewing Heads S650
- Advanced Signal Processors P650
- Signal Processors Model P531 or P532
- View All Discontinued: Burner Management Systems
- Kromschroeder BCU 400 burner control unit
- Automatic burner control units IFS 132B, 135B, 137B
- R4343 Flame Switch
- Ignition Transformers Q652
- Impulse system MPT 700
- Flame detector IFW 15
- Flame detector for continuous operation IFW 50
- Automatic burner control units PFS 778, 748
- Flame detectors PFF
- Ultraviolet Flame Detector C7927
- Ultraviolet Flame Detector C7961E,F
- Automatic burner control units for continuous operation PFD 778
- Automatic burner control units IFS 110IM, 111IM
- IFD 450, 454
- View All Manual Valves & Filters
- Manual valves AKT
- Manual valves with thermal equipment trip AKT..TAS
- Thermal equipment trips TAS
- Gas-filters GFK
- A Style Synchro Valves
- Disc Type Check Valves
- Flow adjusting cocks GEHV, GEH, LEH
- Manual Shutoff Valves
- Shut off valves ZIVA
- Adjustable Orifice Valves (ALO/ALO-R)
- View All Pressure Regulators
- Pressure regulators for gas J78R, 60DJ
- Pressure regulators for gas GDJ
- Pressure regulators for gas VGBF
- Safety shut-off valves JSAV
- Relief valve VSBV
- Variable air/gas ratio controls GIKH
- Circulation pressure control and relief regulators VAR
- Gas Pressure Regulators Maxon
- Air/gas ratio controls GIK
- View All Shutoff Valves
- Series 8000 Air Actuated Safety Shut-off Valves for Fuel Gas Service
- Series 8000 Air Actuated Safety Shutoff Valves for Liquid Service
- High Pressure Electro-Mechanical Gas Safety Shut-off Valves
- High Pressure Electro-Mechanical Oil Safety Shut-off Valves
- NI Series Hazardous Location Safety Shut-off Valves
- V5097 Integrated gas valve train
- V48/V88 Diaphragm gas valves
- V4943/V8943 Single-stage pressure regulating valves
- V4944B, L, N/8944B, C, L, N Two-stage pressure regulating gas valves
- V5055 Industrial gas valves, V4055 Fluid power actuators
- V4062 Fluid power actuators
- Solenoid valves for gas VGP
- Solenoid valves for gas VG
- Motorized valves for gas VK
- Solenoid valves for gas VE, V4295
- VQ400/800 Series
- V4046/V8046 Pilot gas valves
- View All Butterfly Valves & Actuators
- BV-Pak
- Butterfly valves BVG, BVA, BVH
- Linear flow controls IFC, VFC
- Butterfly valves DKR
- Butterfly Valves
- Solenoid-operated butterfly valves for air MB 7/BVHM
- Wafer Butterfly Valves for Hot Air WBV-H
- Honeywell Slate low torque actuator
- Modutrol Motors
- Kromschröder IC + Valve Assemblies
- Actuators IC
- View All Pressure Switches & Gauges
- Honeywell C6097 pressure switches for gas
- Kromschroeder DL..A pressure switches for air
- Kromschroeder DG pressure switches for gas
- Kromschroeder DL..K pressure switches for air
- Kromschroeder DG..C pressure switches for gas
- Kromschroeder DL..E pressure switches for air
- Elektronic pressure gauge DMG
- Pressuretrol® Limit controllers L4079A, B, W, L604N
- Pressure gauges KFM, RFM
- Pressure Indicators PI
- PressureTrol® Pressure monitoring on/off controllers L404F, T, V
- PressureTrol® Pressure monitoring modulating controllers L91A, B
- CPS
- Pressure switches for gas DGM, DWR
- Vaporstat ® Controllers L408J
-
Services
Services
-
Cybersecurity Services
Highly skilled OT cybersecurity consultants can provide services to support your cybersecurity needs.
-
Fire & Gas Services
Process fire and gas systems play a key role in protecting valuable production assets.
-
Control System Services
Modernize systems, optimize performance, and help mitigate cybersecurity risks.
-
Combustion Services
Technical services and engineered solutions for fuel-fired equipment across all major industries.
-
Training
Honeywell Academy offers a variety of courses to keep your workers updated on the latest technology.
-
Utility Services
Industry services, including: AMI upgrades, gas line locating, and water leak detection.
-
Smart Grid Solutions & Services (SGS)
Comprehensive energy efficiency solutions for the Utility Industry
-
Maintenance Assist
Maintenance Assist is Honeywell’s advanced Generative AI digital assistant designed to streamline maintenance tasks and enhance efficiency.
-
Cybersecurity Services
-
Solutions
Solutions
-
Support
Support
You are browsing the product catalog for
You are viewing the overview and resources for
Get Super Powered with SmartLine
How Remote Monitoring Can Turn Thermal Process Data into Actionable Information
Abhinav Barnwal, Offering Management Lead, Honeywell Thermal Solutions Dale Smith, Global Growth Leader – Connected Services, Honeywell Thermal Solutions
Thermal processing industries need to maximize their productivity sustainably. There is a growing need for facility owners and operators to improve productivity by minimizing unplanned downtime. In today’s competitive business climate, production and process systems must deliver value by operating in the smartest, most efficient and most sustainable manner possible.
Companies that don’t leap to a modern, integrated automation system, risk high energy costs for day-to-day operations, the safety of equipment and personnel; and penalties for failing to meet environmental standards. Isolated, purpose-built solutions for process control also make it difficult to increase production to meet growing customer demand.
Furthermore, the widespread global disruption caused by the coronavirus underscores the importance of being able to monitor and manage installations remotely if personnel are not able to travel to them.
How can the latest integrated technology solutions help optimize thermal processes? How can they help connect production assets securely in the cloud for enhanced control and performance monitoring to make critical asset data available anytime, anywhere? How can a new breed of remote monitoring solutions provide valuable insight into critical thermal processes?
Today’s demands and operating challenges
With rising energy costs, reduced profit margins and increasing demand for quality, manufacturers with thermal processing operations need to increase productivity, eliminate safety risks and reduce operating expenses. Their primary objectives include:
· Increasing plant efficiency to drive ROI and reduce energy costs
· Lowering maintenance costs
· Minimizing unplanned downtime to increase the availability of heating systems
· Reducing emissions to reduce the risk of related taxes and fines
· Enhancing safety
· Boosting productivity to meet customer demand
Additionally, in thermal process systems such as boilers, ovens and furnaces; information that is vital to efficiency, safety and reliability – is often trapped at the equipment level. That’s a problem unless a worker is standing in front of the equipment, and even then, it might be too late. Maintenance technicians are frequently required to travel to thermal processing equipment to troubleshoot and diagnose problems, and don’t always know what tools or parts are required until they’re on site. This can result in multiple return trips to address an issue.
Moreover, the retirement of engineers, operators and technicians familiar with industrial process heating, and the reality of millennials changing jobs frequently, is creating a shortage of proven know-how. There are fewer combustion specialists across the industry and the plant personnel that remain are being given more responsibilities than ever before.
Need for effective controls
When fewer personnel need to do more work, it’s crucial to optimize process control, which means meeting certain parameters over time by using inputs from process and controlling outputs for desired results. Additionally, the provision of remote access capabilities can help safeguard against the long-term disruption caused by global events, such as the coronavirus. Today’s sophisticated technology overcomes these challenges, allowing users to make better decisions related to process, productivity, quality and safety – even if they’re not on site.
Thermal processing personnel must implement real-time controls to measure and control critical process variables, develop methods to remotely monitor these variables, and find ways to predict future behavior of thermal processes. All types of industrial heating operations depend on state-of-the-art automation technology to stay competitive. Those who resist change will be left behind, wondering why their business is declining and being surpassed by competitors. And those who embrace the opportunity that advanced process control and monitoring systems provide will grow and prosper.
Value of a connected solution
Many companies in the thermal processing industry continue to rely on disparate, purpose-built solutions to run critical production processes. They use components from multiple vendors as well as separate platforms and protocols. Complicated wiring schematics and programming sequences are the norm. With multiple vendor systems in place, process steps might include manual data exchange between systems, thereby increasing processing times and the risk of failure. It’s hard to monitor and control a process when it is fragmented across incompatible solutions.
Conversely, the implementation of a single, connected architecture for industrial heating reduces the control “footprint” in most facilities and enables remote monitoring and troubleshooting of crucial production equipment. With control strategies supported by a single integrated solution, all stakeholders are connected through one automated workflow and access to the same data. The process is continuously monitored, with alerts of any deviations.
By taking an integrated system approach, manufacturers can realize the benefits of improved operator effectiveness, increased plant availability, reduced maintenance costs and lower lifecycle costs. They can also leverage the Industrial Internet of Things (IIoT) to improve the safety, efficiency and reliability of operations across a single plant or several plants of an enterprise.
An IIoT infrastructure provides secure methods to capture and aggregate data and apply advanced analytics. Furthermore, it leverages domain expertise and allows end users to use the information to determine methods to reduce or even eliminate manufacturing upsets and inefficiencies. With a large, consolidated set of data provided by experts who understand the unique characteristics of thermal processing applications, manufacturers can apply higher-level analytics for more detailed insight and scale data to meet the varied needs of single-site or enterprise-wide operations.
Putting technology to work
Thermal processing companies can harness the power of connectivity and information sharing to transform their operations. They can use connected devices and integrated systems to capture real-time process information to:
· Improve asset productivity through a better understanding of their equipment
· Identify variability across production processes
· Establish remote monitoring and operational capabilities
· Implement manufacturing best practices
· Enhance safety and regulatory compliance
· Automate repetitive reporting to improve productivity
Industrial heating operations now have access to innovative automation solutions that are focused on turning data into insight – from edge to enterprise – to help improve their bottom line.
For example, Honeywell’s new SLATE™ Combustion Equipment Manager combines configurable safety features with programmable logic in a single, modular burner control platform. The system reduces the footprint of control room panels and can be easily customized for virtually any combustion application, in less time – and with far less complexity – than traditional solutions. Instead of using separate controllers for different functions, users can simply purchase the modules they need for combustion control and choose how to use them with simple wiring commands. With fewer assets to support and maintain, they can realize lower total cost of ownership.
In conventional control systems, a control panel often contains a programmable logic controller (PLC) combined with separate safety devices such as burner controls. In this case, the safety devices are responsible for the operation and safety of critical equipment. Safety modules operate as discrete, self-contained safety controls.
Previously, data produced by safety devices was connected to whatever the control was doing. If the control function included communication, then the PLC captured and interpreted this information using specialized software. In the latest generation of combustion control systems, all safety module status data and all non-safety control of safety modules are fully integrated into the programmable logic. The base module provides communication and user-programmable logic, while non-safety digital and analog I/O modules provide inputs and outputs for logic. The programmable logic can be used to create any non-safety features required by the equipment that the combustion control system is controlling. This allows an application designer to implement customized, differentiated features in a controller using a configurable touch screen display.
SLATE can also use microprocessor-based burner control platforms, including SIL-3 capable solutions for sequencing multiple burners. Additionally, it can incorporate DIN-mounted universal digital controllers that provide functionality for set point programming, fast scanning and on-board diagnostics. Users can even install intelligent valves designed to communicate with industrial automation systems for enhanced monitoring, reporting and optimization.
Need to make data visible
Most maintenance managers are acquainted with the panic associated with handling critical thermal process failure and investigating potential causes after the incident. In many cases, the issues may require repairs and eventually cause potential unplanned downtime. In order to unleash greater productivity, industrial operations of all sizes are looking for ways to improve the visibility of asset and production issues. Experience has shown that unplanned downtime can result in significant lost revenue. Shutdowns can also lead to substantial response and recovery costs, labor and overhead costs, customer service impact and more.
What factory workers need is an effective way to view and share data before they get to the equipment. This includes mobility tools that enable them to receive real-time alerts when operating parameters exceed limits and track historical data to see when and why issues occurred.
Honeywell’s Thermal IQ™ platform
Honeywell’s response to industry demand for better remote process and equipment monitoring capabilities is Thermal IQ, a platform designed for organizations with limited or no tracking or remote access capabilities and that consequently cannot optimize their thermal process systems.
The solution is also ideal for global organizations with facilities spread across multiple regions that want to bring their operations more tightly together.
Consisting of wireless cellular connectivity, a mobile application and an enterprise-view dashboard, the Thermal IQ platform securely connects combustion equipment to the cloud, making critical thermal process data that is normally confined at the equipment level available anytime, anywhere, on any smart device or desktop.
With Thermal IQ data, users can closely monitor thermal processes without being on site, get real-time alerts when key parameters stray outside normal limits, track historical data over time to identify when and why something happened and provide actionable recommendations. In other words, Thermal IQ turns thermal process data into actionable information.
Built from the ground up with security in mind, the Thermal IQ platform offers a superior level of cyber protection. It uses cybersecurity best practices and the latest security techniques to mitigate threats and further that communication channels are strictly controlled.
Honeywell offers two different solutions based on the Thermal IQ platform: Thermal IQ Operate, an equipment- and process-level remote monitoring solution that provides process operators with real-time asset performance data on smart devices; and Thermal IQ Optimize, an enterprise-level, desktop-based remote monitoring solution that delivers real-time analytics and fault modelling with early event detection.
Platform architecture
Plant combustion equipment management systems and edge devices such as Honeywell Combustion Controls or existing field sensors at equipment, site and regional level capture and communicate key parameters to 4G cellular gateways, which, in turn, transfer data to a secure cloud platform.
Captured field data is then processed in the cloud to generate critical parameters, alarms and trends – revealing insights on thermal processes which can be visualized by users on respective dashboards accessible on mobile devices and desktop computers. Depending on which Thermal IQ platform is being used, deeper, real-time analysis can be extracted, including fault and root cause analysis, predictive analysis and recommendations. Armed with these insights, users can take appropriate, immediate actions to optimize the health of their thermal process equipment.
Thermal IQ™ Operate and its benefits for process operators
Designed for process operators on the move, Thermal IQ Operate is a remote monitoring solution that provides timely, real-time thermal performance information to users via smartphones and devices.
Users get a high-level view of how their equipment is performing and can quickly and easily drill down into individual pieces of equipment to see current alerts and status of key parameters.
They can also compare processes and system performance across the enterprise to identify non-performing assets, which can then be investigated and optimized to bring their performance up to the level of the best-performing assets.
Users can stay ahead of faults or potential failures that can lead to downtime with early alerts. That visibility also enables technicians to arrive at the equipment with the correct tools to repair the problem, while reducing maintenance costs.
With the capability to track historical data by day, week or month to identify trends and opportunities for improvement, Thermal IQ Operate connects everyone from management to maintenance with insights that drive smarter decisions, such as improving the competency and productivity of people, the efficiency of processes and the performance of assets.
Here is an example to illustrate the power of mobile remote access. A global building material manufacturer deployed Thermal IQ and could identify a performance difference when using a dual flame detector system. This user noted the marginal operation of one flame detector when comparing its performance with the dual system on the same application. The user scheduled maintenance operation on the furnace and a simple cleaning of the flame detector viewing lens returned the system to proper operation while avoiding an unplanned production stoppage.
Thermal IQ™ Optimize and its benefits for enterprises
Designed for enterprise desktop use, Thermal IQ Optimize provides real-time analytics and fault modeling with early event detection at plant, equipment and process level to keep thermal equipment running safely, efficiently and effectively.
Based on Honeywell Forge asset and process performance models, the solution extracts data from combustion equipment and thermal processes across the enterprise and delivers a clear, high-level view of thermal process performance via cascading performance dashboards which use the latest visual analytics.
Thermal IQ Optimize processes and measures data in four categories – safety, performance, reliability and efficiency – with the help of inbuilt algorithms that allow users to understand both the health and business cases of their assets at site, division and global level. Users can compare and benchmark equipment data to see which pieces of equipment, sites or regions are performing or failing and then take actions to boost performance levels accordingly.
Using intuitive, interactive fault tree analysis, users can drill into the data of individual assets for an in-depth analysis, enabling them to quickly and easily identify anomalies in equipment functionality or processes, determine their impact on enterprise efficiency and operate before failures occur.
To understand how Thermal IQ Optimize works in practice, let’s quickly examine a case involving a manufacturing site in Muncie, Indiana. There, persistent issues with short-cycling caused additional wear via thermal fatigue stress and excessive valve actuation, as well as reductions in efficiency. Thermal IQ enabled multiple potential causes of the short-cycling to be narrowed to a single root cause. Addressing it not only reduced the short-cycling of the boiler – but also resulted in an efficiency gain of up to 5%.
Conclusion
The latest advances in remote monitoring are freeing personnel from the burden of local equipment monitoring and unleashing facilities’ thermal process potential to drive performance and productivity by connecting people, assets and information across the enterprise.
From the simplest use cases – such as viewing asset data on smartphone or laptop – to more sophisticated applications such as sending real-time notifications when an alarm occurs, connected thermal process solutions are revolutionizing the way process operations run and maintain vital thermal process systems.
Rather than having to integrate, support and maintain purpose-built solutions for combustion control and monitoring, thermal processing operations can now be run more efficiently to optimize production and business results.
Copyright © 2025 Honeywell International Inc.
Maximum File Size
Maximum Files Exceeded
Due to inactivity you will be logged out in 000 seconds.
Maximum File Size
Maximum Files Exceeded
Honeywell International Inc. is committed to ensuring compliance with global laws that regulate its export and import activities. In following company procedures, it has been determined that is identified on a denied/restricted parties list that is applicable to this transaction.
As a result, Honeywell is unable to continue with this request.
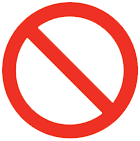