-
Currency:Localize your Content
You can set your preferred currency for this account.
Choose a Currency
Currency- CHOOSE YOUR CURRENCY
Update Currency
Changing Currency will cause your current cart to be deleted. Click OK to proceed.
To Keep your current cart, click CLOSE and then save your cart before changing currency.
-
Select Account
Switching accounts will update the product catalog available to you. When switching accounts, your current cart will not move to the new account you select. Your current cart will be available if you log back into this account again.
Account# Account Name City Zip/Post Code CANCELPROCEEDMy Account -
-
Products
- View All Control & Supervisory Systems
- Control & Supervisory Systems Parts & Accessories
- Distributed Control Systems (DCS)
- Safety Systems
- SCADA
- Quality Control Systems (QCS)
- Modular Controllers
- Human Machine Interfaces (HMI)
- Remote Terminal Units (RTU)
- Drives
- Modular Systems Remote IO
- Discrete Automation Solutions
- View All Field Instruments
- Pressure Transmitters
- Temperature Transmitters
- Multivariable Transmitters
- Wireless Transmitters
- Level Transmitters
- Flow Meters
- Honeywell Versatilis™ IOT Sensor Solutions
- RMA Remote Meter Assemblies
- Field Instruments Configuration Tools and Software
- Discontinued: Field Instruments
- View All Discontinued: Field Instruments
- SmartLine RM Series - Guided Level Meters
- SmartLine RM Series - Non-Contact Radar Level Meter
- XYR 6000 Absolute Pressure
- XYR 6000 Differential Pressure
- XYR 6000 Discrete I/O
- XYR 6000 Gauge Pressure
- XYR 6000 High Level Analog Input Transmitter
- XYR 6000 Temperature Transmitters
- XYR 6000 Universal I/O
- View All Regulators & Safety Accessories
- High Pressure Regulators up to ANSI 600
- High Pressure Regulators up to PN40 (ANSI 300)
- Medium Pressure Regulators up to PN16 (ANSI 150)
- Pilot Heater
- Safety Relief Valves
- Safety Shut-Off Valves
- Series 200 Small Pressure Regulators (Pressure Reducer)
- Series 600 Control Equipment for Safety Shut-Off Valves
- Series 600 Pilot Regulators for Pilot operated Gas Pressure Regulators
- Series 900 - Gas filters/Valves and other Components
- Regulators & Safety Accessories Spare Parts
- View All Fixed Gauging
- PL3700X Pressure and Level Transmitters
- EM540 & EM940 Radar Level Gauge
- T901 Temperature and Pressure Transmitters
- Lidec Liquid Level Switch
- CT801 Electropneumatic Level Transmitters
- Communication Interface Unit
- CargoBoss Tank Gauging Software
- Q96 Analog Indicator
- Spare Parts & Accessories - Marine Fixed Gauging
- View All Portable Sampling
- HERMetic Sampler GT & Sampler GT Chem for Marine Applications
- HERMetic Sampler GT1 for Marine Applications
- HERMetic Sampler GTX for Marine Applications
- HERMetic Sampler GTN for Marine Applications
- HERMetic Sampler GT4 for Marine Applications
- Gauging and Sampling for high-pressure Tankers
- HERMetic Samplers for Restricted Operations
- Spare Parts - Marine Portable Gauging & Sampling
- Ballast Water Sampler
- View All Marine Pressure Transmitters
- SmartLine STF800 - Flange Mount
- SmartLine STA800 - Absolute Pressure
- Absolute Pressure Transmitter - SmartLine STA700
- Remote Diaphragm Transmitters - SmartLine STR700
- SmartLine STR800 - Remote Diaphragm
- SmartLine STD800 - Differential Pressure
- Differential Pressure Transmitter - SmartLine STD700
- Gauge Pressure Transmitters - SmartLine STG700
- SmartLine STG800 - Gauge Pressure
- Flange Mount Transmitters - SmartLine STF700
- View All Discontinued: Process Instruments
- DCP50 DIN Programmer
- DL4000 Conductivity Cells
- DL5000 Equilibrium Probe
- 7774/7774D Insertion/Removal Ball Valve Mounting
- 7777/7777D Immersion/In-Line Glass Mounting
- 7777DVP Immersion/In-Line Mounting
- DL1000 Durafet Mountings
- DL2000 Meredian Glass Mountings
- DL3000 ORP Mountings
- HB and HBD Series Ruggedized Electrodes
- DR4300 Circular Chart Recorder
- UDC700 DIN Controller
- Process Instrument Explorer (PIE) Software
- Honeywell’s Chamber IQ
- 4905 Immersion or Flow Thru Mounting
- 4909 Ball Valve or Insertion Mounting
- 4973 Flow Thru Mounting
- View All Portable Gauging & Sampling for Land Applications
- HERMetic UTImeter Gtex 2000 - Closed Type - Land Applications
- HERMetic UTImeter Otex - Restricted Type - Land Applications
- HERMetic Sampler GT & Sampler GT Chem - Land Applications
- HERMetic Sampler GTX Chem - Land Applications
- HERMetic Sampler GTN Chem - Land Applications
- HERMetic Sampler GT4 - Land Applications
- HERMetic Sampler A-2 and A-4 - Land Applications
- View All Burners & Heat Exchangers
- Direct Fired Furnace Burners
- Self-Recuperative and Radiant Tube Burners
- Single Burners
- Line & Duct Burners
- Glass & Oxygen Burners
- Immersion Tube Burners
- Hauck Asphalt Burners
- Exothermics Heat Exchangers & Indirect Air Heaters
- Pre-Mix Equipment
- Pilot Burners
- Burner Accessories
- Discontinued: Burners & Heat Exchangers
- View All SmartLine ST700 Pressure Transmitters
- Flange Mount Transmitters - SmartLine STF700
- Gauge Pressure Transmitters - SmartLine STG700
- Absolute Pressure Transmitter - SmartLine STA700
- Flush Mount Pressure Transmitters - SmartLine ST700
- Remote Diaphragm Transmitters - SmartLine STR700
- Differential Pressure Transmitter - SmartLine STD700
- View All Meter Hardware & Accessories
- Hand Tools and Toolkits
- Needle Valves
- Swivel Washers
- Pete's Plugs
- Differential Pressure Testers
- Gas Leak Detectors
- Shut-Off Seals
- Batteries
- Meter Nuts
- Manometers
- M201E DP Tester
- Paint Covers
- Pressure Gauges
- Lubrication & Oil
- Meter Swivels
- Dust Caps
- Straightening Vanes
- Meter Connections
- Critical Flow Provers
- Meter Adapters
- Pulsers & Displays
- Flange Covers
- Splashguards
- View All Discontinued: Burners & Heat Exchangers
- EcoStar IIB
- ImmersoPak
- Blast Tips
- Eclipse Pilots
- ThermJet Self-Recuperative Burner
- WIDE-RANGE®
- CCTV
- ValuPak
- GTCPA
- OvenPak II
- Delta-TE
- GT-NG
- 780P
- Kinedizer
- ExtensoJet
- MultiFire
- Forehearth Burners
- Sealed Nozzle
- SVG
- Oxy-Therm® FH
- LP, Tee, Vari-Set Mixers
- WRASP
- INCINO-PAK®
- CYCLOMAX®
- 03FA
- AirJector
- Brightfire (Original)
- View All Burner Control Units
- Honeywell 7800 SERIES burner control unit
- Honeywell SLATE combustion management system
- Burner control unit BCU 570
- Burner control units BCU 560, BCU 565, BCU 580
- Automatic burner control units PFU
- Protective system control FCU
- Kromschroeder IFD 258 burner control unit
- Kromschroeder IFD 244 burner control unit
- SOLA
- Legacy Burner Management Systems
- BCU 4 (Next Generation)
- Burner control unit BCU 370
- View All Industrial Flame Monitoring (IFM)
- Flare Stack Monitoring System Watchdog III
- Industrial Flame Monitoring Accessories
- Gas Igniters GHE
- Viewing Heads S70X/S80X
- FASA Glass and Quartz Fiber Optics
- Signal Processors Model P522
- Signal Processors Model 600U
- Viewing Heads S55XBE
- Viewing Heads U2
- Signal Processors Model 700SP
- FlameTools or Thermalsoft Configuration Tools
- Advanced Viewing Heads S650
- Advanced Signal Processors P650
- Signal Processors Model P531 or P532
- View All Discontinued: Burner Management Systems
- Kromschroeder BCU 400 burner control unit
- Automatic burner control units IFS 132B, 135B, 137B
- R4343 Flame Switch
- Ignition Transformers Q652
- Impulse system MPT 700
- Flame detector IFW 15
- Flame detector for continuous operation IFW 50
- Automatic burner control units PFS 778, 748
- Flame detectors PFF
- Ultraviolet Flame Detector C7927
- Ultraviolet Flame Detector C7961E,F
- Automatic burner control units for continuous operation PFD 778
- Automatic burner control units IFS 110IM, 111IM
- IFD 450, 454
- View All Manual Valves & Filters
- Manual valves AKT
- Manual valves with thermal equipment trip AKT..TAS
- Thermal equipment trips TAS
- Gas-filters GFK
- A Style Synchro Valves
- Disc Type Check Valves
- Flow adjusting cocks GEHV, GEH, LEH
- Manual Shutoff Valves
- Shut off valves ZIVA
- Adjustable Orifice Valves (ALO/ALO-R)
- View All Pressure Regulators
- Pressure regulators for gas J78R, 60DJ
- Pressure regulators for gas GDJ
- Pressure regulators for gas VGBF
- Safety shut-off valves JSAV
- Relief valve VSBV
- Variable air/gas ratio controls GIKH
- Circulation pressure control and relief regulators VAR
- Gas Pressure Regulators Maxon
- Air/gas ratio controls GIK
- View All Shutoff Valves
- Series 8000 Air Actuated Safety Shut-off Valves for Fuel Gas Service
- Series 8000 Air Actuated Safety Shutoff Valves for Liquid Service
- High Pressure Electro-Mechanical Gas Safety Shut-off Valves
- High Pressure Electro-Mechanical Oil Safety Shut-off Valves
- NI Series Hazardous Location Safety Shut-off Valves
- V5097 Integrated gas valve train
- V48/V88 Diaphragm gas valves
- V4943/V8943 Single-stage pressure regulating valves
- V4944B, L, N/8944B, C, L, N Two-stage pressure regulating gas valves
- V5055 Industrial gas valves, V4055 Fluid power actuators
- V4062 Fluid power actuators
- Solenoid valves for gas VGP
- Solenoid valves for gas VG
- Motorized valves for gas VK
- Solenoid valves for gas VE, V4295
- VQ400/800 Series
- V4046/V8046 Pilot gas valves
- View All Butterfly Valves & Actuators
- BV-Pak
- Butterfly valves BVG, BVA, BVH
- Linear flow controls IFC, VFC
- Butterfly valves DKR
- Butterfly Valves
- Solenoid-operated butterfly valves for air MB 7/BVHM
- Wafer Butterfly Valves for Hot Air WBV-H
- Honeywell Slate low torque actuator
- Modutrol Motors
- Kromschröder IC + Valve Assemblies
- Actuators IC
- View All Pressure Switches & Gauges
- Honeywell C6097 pressure switches for gas
- Kromschroeder DL..A pressure switches for air
- Kromschroeder DG pressure switches for gas
- Kromschroeder DL..K pressure switches for air
- Kromschroeder DG..C pressure switches for gas
- Kromschroeder DL..E pressure switches for air
- Elektronic pressure gauge DMG
- Pressuretrol® Limit controllers L4079A, B, W, L604N
- Pressure gauges KFM, RFM
- Pressure Indicators PI
- PressureTrol® Pressure monitoring on/off controllers L404F, T, V
- PressureTrol® Pressure monitoring modulating controllers L91A, B
- CPS
- Pressure switches for gas DGM, DWR
- Vaporstat ® Controllers L408J
-
Services
Services
-
Cybersecurity Services
Highly skilled OT cybersecurity consultants can provide services to support your cybersecurity needs.
-
Fire & Gas Services
Process fire and gas systems play a key role in protecting valuable production assets.
-
Control System Services
Modernize systems, optimize performance, and help mitigate cybersecurity risks.
-
Combustion Services
Technical services and engineered solutions for fuel-fired equipment across all major industries.
-
Training
Honeywell Academy offers a variety of courses to keep your workers updated on the latest technology.
-
Utility Services
Industry services, including: AMI upgrades, gas line locating, and water leak detection.
-
Smart Grid Solutions & Services (SGS)
Comprehensive energy efficiency solutions for the Utility Industry
-
Maintenance Assist
Maintenance Assist is Honeywell’s advanced Generative AI digital assistant designed to streamline maintenance tasks and enhance efficiency.
-
Cybersecurity Services
-
Solutions
Solutions
-
Support
Support
You are browsing the product catalog for
You are viewing the overview and resources for
Get Super Powered with SmartLine
Hydrogen: An Opportunity to Reduce Industrial CO2Emissions
By Todd Ellerton, Director of Offering Management, Honeywell Thermal Solutions
To date, the mainstream application of hydrogen has been held back by a variety of factors, including a lack of infrastructure, limited production capabilities, high costs and unique properties that make the element tricky to handle. However, the balance is now tipping toward a hydrogen-propelled future.
One fundamental challenge has been how to safely transport and store hydrogen, which has a wide flammability range compared to natural gas. Natural gas is flammable between 4 and 16 vol% gas in a gas and air mixture, while hydrogen is flammable between 4 to 77 vol% hydrogen in an equivalent mixture.
Whereas suitable infrastructure was limited in the past, new transmission networks and storage facilities are now being built to accommodate hydrogen. Moreover, energy companies are realizing that their natural gas grids can be adapted to accommodate hydrogen at reasonable cost. Europe, for instance, has a vast gas grid that could be converted relatively quickly, and there are separate initiatives underway in Scotland and Australia, for example, to build 100% green hydrogen-powered energy grids.
Then there’s the high cost of hydrogen which has traditionally deterred energy companies from taking it seriously. But today its cost is falling, and it’s expected to continue to do so over the next decade. This year, the Hydrogen Council said it expects hydrogen to be competitive across 22 industry applications with other low-carbon alternatives and even some conventional energy sources by 2030 .A further challenge to hydrogen has been the lack of machinery and components from which to harness it for the manufacturing of goods –specifically, via thermal appliances in which heat is required. However, companies such as Honeywell Thermal Solutions are rapidly expanding their solution portfolios to encompass hydrogen-ready burners, valves, combustion controls and other specialty equipment.
A final challenge is that nitrogen oxide (NOX) emissions produced with hydrogen combustion, in general, are greater than with natural gas due to faster flame speeds and higher flame temperatures associated with hydrogen. Typically, NOX increases steadily as the amount of hydrogen increases in the blend with natural gas up to about 60% hydrogen. The impact on NOX can become quite dramatic for blends with more than 60% hydrogen, depending on burner design. Regulations on NOX emissions are growing stricter and more widespread as well. The convergence of CO2 and NOX emission regulations will likely necessitate the development of new combustion technologies once higher concentrations of hydrogen achieve broader adoption.
Exploiting the potential of hydrogen—with care
In addition to the technical and cost barriers of hydrogen production, hydrogen requires specialist know-how to harness its potential. It must be handled differently to other fuels, with a wide range of precautions taken to process it safely.
Because of hydrogen’s wide flammability range, combustion systems must be designed differently than those of natural gas. They must undergo extensive risk assessments at both proposal and execution phases to help them meet hydrogen application safety requirements and comply with local safety codes and standards. In addition, hydrogen’s high flame speed and low ignition temperature require proper electrical design and wiring principles to be followed, with special attention paid to purging, ratio-control, temperature protection and burner management functions. Knowing a burner can fire safely and reliably on hydrogen is one thing; knowing its effect on an application is another. When firing a burner on hydrogen, the combustion characteristics are different compared to the same burner firing on natural gas. The differences in flammability, speed of the combustion reaction, flame luminosity, flame length and changes in flue gas composition all impact how products are heated and how combustion chambers or ovens should be constructed to accommodate them. Burners should be test-fired on hydrogen and the integrity of components such as mixing plates, mixing cones, gas nozzle materials and ports checked to foster that hydrogen combustion remains stable and safe without overheating or even destroying parts of the equipment.
Conclusion
Hydrogen is rapidly emerging from the shadows to present a viable solution to reducing global CO2emissions. Governments are seeing the potential for hydrogen to decarbonize sectors that were once considered too complex for transformation, such as transportation, freight and logistics, industrial heating and industry feedstock. At the same time, companies within oil and gas, chemicals, heating and automotive and other sectors now regard hydrogen as a credible way to achieve long-term sustainability objectives.
Today, climate change impact, diminishing barriers to adoption and better industry understanding of how to handle hydrogen safely and harness its potential, are pointing to a potentially hydrogen-driven, carbon-neutral future for us all.
Copyright © 2025 Honeywell International Inc.
Maximum File Size
Maximum Files Exceeded
Due to inactivity you will be logged out in 000 seconds.
Maximum File Size
Maximum Files Exceeded
Honeywell International Inc. is committed to ensuring compliance with global laws that regulate its export and import activities. In following company procedures, it has been determined that is identified on a denied/restricted parties list that is applicable to this transaction.
As a result, Honeywell is unable to continue with this request.
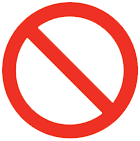