-
Currency:Localize your Content
You can set your preferred currency for this account.
Choose a Currency
Currency- CHOOSE YOUR CURRENCY
Update Currency
Changing Currency will cause your current cart to be deleted. Click OK to proceed.
To Keep your current cart, click CLOSE and then save your cart before changing currency.
-
Select Account
Switching accounts will update the product catalog available to you. When switching accounts, your current cart will not move to the new account you select. Your current cart will be available if you log back into this account again.
Account# Account Name City Zip/Post Code CANCELPROCEEDMy Account -
-
Products
- View All Control & Supervisory Systems
- Control & Supervisory Systems Parts & Accessories
- Distributed Control Systems (DCS)
- Safety Systems
- SCADA
- Quality Control Systems (QCS)
- Modular Controllers
- Human Machine Interfaces (HMI)
- Remote Terminal Units (RTU)
- Drives
- Modular Systems Remote IO
- Discrete Automation Solutions
- View All Field Instruments
- Pressure Transmitters
- Temperature Transmitters
- Multivariable Transmitters
- Wireless Transmitters
- Level Transmitters
- Flow Meters
- Honeywell Versatilis™ IOT Sensor Solutions
- RMA Remote Meter Assemblies
- Field Instruments Configuration Tools and Software
- Discontinued: Field Instruments
- View All Discontinued: Field Instruments
- SmartLine RM Series - Guided Level Meters
- SmartLine RM Series - Non-Contact Radar Level Meter
- XYR 6000 Absolute Pressure
- XYR 6000 Differential Pressure
- XYR 6000 Discrete I/O
- XYR 6000 Gauge Pressure
- XYR 6000 High Level Analog Input Transmitter
- XYR 6000 Temperature Transmitters
- XYR 6000 Universal I/O
- View All Regulators & Safety Accessories
- High Pressure Regulators up to ANSI 600
- High Pressure Regulators up to PN40 (ANSI 300)
- Medium Pressure Regulators up to PN16 (ANSI 150)
- Pilot Heater
- Safety Relief Valves
- Safety Shut-Off Valves
- Series 200 Small Pressure Regulators (Pressure Reducer)
- Series 600 Control Equipment for Safety Shut-Off Valves
- Series 600 Pilot Regulators for Pilot operated Gas Pressure Regulators
- Series 900 - Gas filters/Valves and other Components
- Regulators & Safety Accessories Spare Parts
- View All Fixed Gauging
- PL3700X Pressure and Level Transmitters
- EM540 & EM940 Radar Level Gauge
- T901 Temperature and Pressure Transmitters
- Lidec Liquid Level Switch
- CT801 Electropneumatic Level Transmitters
- Communication Interface Unit
- CargoBoss Tank Gauging Software
- Q96 Analog Indicator
- Spare Parts & Accessories - Marine Fixed Gauging
- View All Portable Sampling
- HERMetic Sampler GT & Sampler GT Chem for Marine Applications
- HERMetic Sampler GT1 for Marine Applications
- HERMetic Sampler GTX for Marine Applications
- HERMetic Sampler GTN for Marine Applications
- HERMetic Sampler GT4 for Marine Applications
- Gauging and Sampling for high-pressure Tankers
- HERMetic Samplers for Restricted Operations
- Spare Parts - Marine Portable Gauging & Sampling
- Ballast Water Sampler
- View All Marine Pressure Transmitters
- SmartLine STF800 - Flange Mount
- SmartLine STA800 - Absolute Pressure
- Absolute Pressure Transmitter - SmartLine STA700
- Remote Diaphragm Transmitters - SmartLine STR700
- SmartLine STR800 - Remote Diaphragm
- SmartLine STD800 - Differential Pressure
- Differential Pressure Transmitter - SmartLine STD700
- Gauge Pressure Transmitters - SmartLine STG700
- SmartLine STG800 - Gauge Pressure
- Flange Mount Transmitters - SmartLine STF700
- View All Discontinued: Process Instruments
- DCP50 DIN Programmer
- DL4000 Conductivity Cells
- DL5000 Equilibrium Probe
- 7774/7774D Insertion/Removal Ball Valve Mounting
- 7777/7777D Immersion/In-Line Glass Mounting
- 7777DVP Immersion/In-Line Mounting
- DL1000 Durafet Mountings
- DL2000 Meredian Glass Mountings
- DL3000 ORP Mountings
- HB and HBD Series Ruggedized Electrodes
- DR4300 Circular Chart Recorder
- UDC700 DIN Controller
- Process Instrument Explorer (PIE) Software
- Honeywell’s Chamber IQ
- 4905 Immersion or Flow Thru Mounting
- 4909 Ball Valve or Insertion Mounting
- 4973 Flow Thru Mounting
- View All Portable Gauging & Sampling for Land Applications
- HERMetic UTImeter Gtex 2000 - Closed Type - Land Applications
- HERMetic UTImeter Otex - Restricted Type - Land Applications
- HERMetic Sampler GT & Sampler GT Chem - Land Applications
- HERMetic Sampler GTX Chem - Land Applications
- HERMetic Sampler GTN Chem - Land Applications
- HERMetic Sampler GT4 - Land Applications
- HERMetic Sampler A-2 and A-4 - Land Applications
- View All Burners & Heat Exchangers
- Direct Fired Furnace Burners
- Self-Recuperative and Radiant Tube Burners
- Single Burners
- Line & Duct Burners
- Glass & Oxygen Burners
- Immersion Tube Burners
- Hauck Asphalt Burners
- Exothermics Heat Exchangers & Indirect Air Heaters
- Pre-Mix Equipment
- Pilot Burners
- Burner Accessories
- Discontinued: Burners & Heat Exchangers
- View All SmartLine ST700 Pressure Transmitters
- Flange Mount Transmitters - SmartLine STF700
- Gauge Pressure Transmitters - SmartLine STG700
- Absolute Pressure Transmitter - SmartLine STA700
- Flush Mount Pressure Transmitters - SmartLine ST700
- Remote Diaphragm Transmitters - SmartLine STR700
- Differential Pressure Transmitter - SmartLine STD700
- View All Meter Hardware & Accessories
- Hand Tools and Toolkits
- Needle Valves
- Swivel Washers
- Pete's Plugs
- Differential Pressure Testers
- Gas Leak Detectors
- Shut-Off Seals
- Batteries
- Meter Nuts
- Manometers
- M201E DP Tester
- Paint Covers
- Pressure Gauges
- Lubrication & Oil
- Meter Swivels
- Dust Caps
- Straightening Vanes
- Meter Connections
- Critical Flow Provers
- Meter Adapters
- Pulsers & Displays
- Flange Covers
- Splashguards
- View All Discontinued: Burners & Heat Exchangers
- EcoStar IIB
- ImmersoPak
- Blast Tips
- Eclipse Pilots
- ThermJet Self-Recuperative Burner
- WIDE-RANGE®
- CCTV
- ValuPak
- GTCPA
- OvenPak II
- Delta-TE
- GT-NG
- 780P
- Kinedizer
- ExtensoJet
- MultiFire
- Forehearth Burners
- Sealed Nozzle
- SVG
- Oxy-Therm® FH
- LP, Tee, Vari-Set Mixers
- WRASP
- INCINO-PAK®
- CYCLOMAX®
- 03FA
- AirJector
- Brightfire (Original)
- View All Burner Control Units
- Honeywell 7800 SERIES burner control unit
- Honeywell SLATE combustion management system
- Burner control unit BCU 570
- Burner control units BCU 560, BCU 565, BCU 580
- Automatic burner control units PFU
- Protective system control FCU
- Kromschroeder IFD 258 burner control unit
- Kromschroeder IFD 244 burner control unit
- SOLA
- Legacy Burner Management Systems
- BCU 4 (Next Generation)
- Burner control unit BCU 370
- View All Industrial Flame Monitoring (IFM)
- Flare Stack Monitoring System Watchdog III
- Industrial Flame Monitoring Accessories
- Gas Igniters GHE
- Viewing Heads S70X/S80X
- FASA Glass and Quartz Fiber Optics
- Signal Processors Model P522
- Signal Processors Model 600U
- Viewing Heads S55XBE
- Viewing Heads U2
- Signal Processors Model 700SP
- FlameTools or Thermalsoft Configuration Tools
- Advanced Viewing Heads S650
- Advanced Signal Processors P650
- Signal Processors Model P531 or P532
- View All Discontinued: Burner Management Systems
- Kromschroeder BCU 400 burner control unit
- Automatic burner control units IFS 132B, 135B, 137B
- R4343 Flame Switch
- Ignition Transformers Q652
- Impulse system MPT 700
- Flame detector IFW 15
- Flame detector for continuous operation IFW 50
- Automatic burner control units PFS 778, 748
- Flame detectors PFF
- Ultraviolet Flame Detector C7927
- Ultraviolet Flame Detector C7961E,F
- Automatic burner control units for continuous operation PFD 778
- Automatic burner control units IFS 110IM, 111IM
- IFD 450, 454
- View All Manual Valves & Filters
- Manual valves AKT
- Manual valves with thermal equipment trip AKT..TAS
- Thermal equipment trips TAS
- Gas-filters GFK
- A Style Synchro Valves
- Disc Type Check Valves
- Flow adjusting cocks GEHV, GEH, LEH
- Manual Shutoff Valves
- Shut off valves ZIVA
- Adjustable Orifice Valves (ALO/ALO-R)
- View All Pressure Regulators
- Pressure regulators for gas J78R, 60DJ
- Pressure regulators for gas GDJ
- Pressure regulators for gas VGBF
- Safety shut-off valves JSAV
- Relief valve VSBV
- Variable air/gas ratio controls GIKH
- Circulation pressure control and relief regulators VAR
- Gas Pressure Regulators Maxon
- Air/gas ratio controls GIK
- View All Shutoff Valves
- Series 8000 Air Actuated Safety Shut-off Valves for Fuel Gas Service
- Series 8000 Air Actuated Safety Shutoff Valves for Liquid Service
- High Pressure Electro-Mechanical Gas Safety Shut-off Valves
- High Pressure Electro-Mechanical Oil Safety Shut-off Valves
- NI Series Hazardous Location Safety Shut-off Valves
- V5097 Integrated gas valve train
- V48/V88 Diaphragm gas valves
- V4943/V8943 Single-stage pressure regulating valves
- V4944B, L, N/8944B, C, L, N Two-stage pressure regulating gas valves
- V5055 Industrial gas valves, V4055 Fluid power actuators
- V4062 Fluid power actuators
- Solenoid valves for gas VGP
- Solenoid valves for gas VG
- Motorized valves for gas VK
- Solenoid valves for gas VE, V4295
- VQ400/800 Series
- V4046/V8046 Pilot gas valves
- View All Butterfly Valves & Actuators
- BV-Pak
- Butterfly valves BVG, BVA, BVH
- Linear flow controls IFC, VFC
- Butterfly valves DKR
- Butterfly Valves
- Solenoid-operated butterfly valves for air MB 7/BVHM
- Wafer Butterfly Valves for Hot Air WBV-H
- Honeywell Slate low torque actuator
- Modutrol Motors
- Kromschröder IC + Valve Assemblies
- Actuators IC
- View All Pressure Switches & Gauges
- Honeywell C6097 pressure switches for gas
- Kromschroeder DL..A pressure switches for air
- Kromschroeder DG pressure switches for gas
- Kromschroeder DL..K pressure switches for air
- Kromschroeder DG..C pressure switches for gas
- Kromschroeder DL..E pressure switches for air
- Elektronic pressure gauge DMG
- Pressuretrol® Limit controllers L4079A, B, W, L604N
- Pressure gauges KFM, RFM
- Pressure Indicators PI
- PressureTrol® Pressure monitoring on/off controllers L404F, T, V
- PressureTrol® Pressure monitoring modulating controllers L91A, B
- CPS
- Pressure switches for gas DGM, DWR
- Vaporstat ® Controllers L408J
-
Services
Services
-
Cybersecurity Services
Highly skilled OT cybersecurity consultants can provide services to support your cybersecurity needs.
-
Fire & Gas Services
Process fire and gas systems play a key role in protecting valuable production assets.
-
Control System Services
Modernize systems, optimize performance, and help mitigate cybersecurity risks.
-
Combustion Services
Technical services and engineered solutions for fuel-fired equipment across all major industries.
-
Training
Honeywell Academy offers a variety of courses to keep your workers updated on the latest technology.
-
Utility Services
Industry services, including: AMI upgrades, gas line locating, and water leak detection.
-
Smart Grid Solutions & Services (SGS)
Comprehensive energy efficiency solutions for the Utility Industry
-
Maintenance Assist
Maintenance Assist is Honeywell’s advanced Generative AI digital assistant designed to streamline maintenance tasks and enhance efficiency.
-
Cybersecurity Services
-
Solutions
Solutions
-
Support
Support
You are browsing the product catalog for
You are viewing the overview and resources for
PRODUCTS
UNISIM® DESIGN
UniSim Design is the core steady state flowsheeting environment. It provides an intuitive and interactive process modeling solution that enables engineers to create steady state models through the appropriate selection of thermodynamics properties, feed compositions and conditions; unit, control, and logic operations.
UNISIM DYNAMIC OPTION
UniSim Dynamic Option provides dynamic simulation capability and is fully integrated within the UniSim Design environment. A steady-state model can be easily converted into a dynamic model with the use of the dynamics assistant. The dynamic model offers rigorous and high-fidelity results with a very fine level of equipment geometry and performance details. Special features for dynamic modeling include pressure-flow dynamics, a rich set of control functionality to support process control and detailed process monitoring, cause and effect matrices, and an event scheduler.
UNISIM CASE LINKER
UniSim Case Linker Allows users to link dynamics cases on multiple CPUs.
UNISIM EO (EQUATION ORIENTED)
UniSim EO is a simulation environment under which equations are solved simultaneously to reach solutions faster, making it suitable for both design and optimization applications. An integral part of the UniSim EvOlution platform, the UniSim EO environment leverages Honeywell’s proprietary NOVA solver. This solver is well suited for solving hundreds of thousands of equations with up to a thousand degrees of freedom, so it can be employed to simulate sizeable processes across all industries, for offline and online applications.
UNISIM OPTIMIZE
UniSim Optimize is an option in addition to the optimizer which is offered with UniSim Design. It includes a number of optimization algorithms (SQP, MINLP and NOVA), allowing UniSim Design to handle more complex optimization problems than the Original Optimizer, and a utility for data reconciliation, which allows models to be matched to operational data.
UNISIM REFINING REACTORS
UniSim Refining Reactors are unit operations built within the UniSim EO environment and represent kinetic, medium-high fidelity unit operations that reflect refinery conversion units. The following modules are currently available:
- UniSim Hydrocracker
- UniSim Hydrotreater
- UniSim Catalytic Reformer
- UniSim Isomerization Reactor
- UniSim Alkylation Reactor
The refining reactor modules can be calibrated using engineering data or real plant data, leveraging the data reconciliation utility in UniSim Design. Also, in conjunction with the LP vector generation utility, the refining reactors may be used to generate LP vectors, for use in scheduling and planning tools
UNISIM FLARE
UniSim Flare is a steady state flare and relief network simulator used to design new flare and vent systems from relief valve to flare tip, or to rate existing systems to ensure that they can handle all possible emergency scenarios. UniSim Flare can also be used to debottleneck an existing flare system that no longer meets the need for safe operation in a plant.
UNISIM BLOWDOWN CUSTOMIZE
UniSim Blowdown Customize is a dynamic utility which is used for sizing, rating and material selection of blowdown systems. This technology:
- accurately predicts blowdown system dynamics and complies with the fire method of the API 521 6th edition standard, thus ensuring their designs are safe and reliable
- considers blowdown vessel networks, pipes, and restriction orifices, eliminating assumptions and fudge-factors that result in costly overdesign
- gives the possibility to test blowdown schedules and simulate what-if scenarios throughout the blowdown network, which enables engineering workflow and gives better insight for safety system design.
UNISIM PRS (PRESSURE RELIEF SYSTEM)
UniSim PRS is a standalone tool for the sizing, rating and validation of pressure relief devices (pressure relief valves and rupture disks) and surrounding pipes (including multiple elements of different diameters). It supports gas, liquid or mixed phase fluids (with or without partial disengagement) and a number of relief scenarios. It provides guided assistance and it generates datasheets and reports. It follows the API/NFPA/ASME code requirements for pressure vessels and storage tanks and CGA code requirements for portable containers.
UNISIM SPIRAL WOUND TUBE BUNDLE
UniSim Spiral Wound Tube Bundle Option accurately models complex spiral wound tube bundle exchangers commonly found in LNG production.
UNISIM GASIFIER
UniSim Gasifier Option unlocks the gasifier operation block inside UniSim Design, allowing the user to model these complex units in both steady state and dynamic modes.
UNISIM THERMOWORKBENCH
UniSim ThermoWorkBench provides users with the ability to create and analyze thermodynamic packages by regressing parameters against laboratory data and for analyzing the resulting predicted phase equilibria behavior. These packages may then be used in UniSim Design or other application using UniSim Thermo. UniSim ThermoWorkbench also allows users to perform azeotropic calculations for multiple compound systems, and to view results using a number of different graphical tools such as Txy and ternary phase equilibria diagrams.
UNISIM EXCHANGERNET
UniSim ExchangerNet is an advanced tool for the design and optimization of heat exchanger networks, pinch analysis, and capital and operational cost optimization.
UNISIM EXCHANGERNET OPERATIONS OPTION
UniSim ExchangerNet Operations Option module may be used to monitor the plant operation of the heat-exchanger networks and understand the impact of different modes of operation on operating costs.
UNISIM HEAT EXCHANGERS
UniSim Heat Exchangers is a suite of products that allow thermal specialists to design, check, simulate, and rate heat exchange equipment rigorously. Used on their own, they enable the determination of the optimum heat exchanger configuration that satisfies all process constraints. Integrated with UniSim Design, opportunities for capital savings in the overall process design may be identified. These products are the result of over 35 years of industry collaboration and research. The heat exchanger products offered in this suite include:
- UniSim Shell-Tube Exchanger Modeler (STE) – For the detailed thermal design, checking or simulation of shell and tube heat exchangers
- UniSim Cross Flow Exchanger Modeler (CFE) - For modeling cross-flow (air-cooled and heat recovery) heat exchangers.
- UniSim Plate-Fin Exchanger Modeler (PFE) - For modeling multi-stream plate-fin heat exchangers made from brazed aluminum, stainless, steel or titanium
- UniSim Fired Process Heater (FPH) - For modeling gas or oil- fired process heaters
- UniSim Plate Heat Exchanger Modeler (PHE) - For modeling plate heat exchanges (gasketed, frame, welded, brazed)
- UniSim Feedwater Heater Modeler (FWH) - For modeling power plant feedwater heaters
- UniSim Process Pipeline Modeler (PPL) - For designing and checking the performance of unbranched pipeline systems carrying single-phase or two-phase fluids.
3RD PARTY PRODUCTS LINKED TO UNISIM DESIGN
UniSim Design can be linked to several technologies developed by our partners. Some of them are directly commercialized by Honeywell, and are available for our customers within the Unisim Design Suite install package. They require a specific license to run (supplied by Honeywell), provided customer has the entitlement to run such 3rd party product within their software license agreement.
CONTACT US
Copyright © 2025 Honeywell International Inc.
Maximum File Size
Maximum Files Exceeded
Due to inactivity you will be logged out in 000 seconds.
Maximum File Size
Maximum Files Exceeded
Honeywell International Inc. is committed to ensuring compliance with global laws that regulate its export and import activities. In following company procedures, it has been determined that is identified on a denied/restricted parties list that is applicable to this transaction.
As a result, Honeywell is unable to continue with this request.
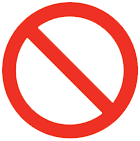